OK - looking for tips / tricks / advice here...
"Someone" snapped the tip of an allen wrench off in the front screw of their Buckmark's site mounting plate (see image below)... Must have been a cheap Chinese tool because there was really very little force applied and it had only deflected a couple of degrees when it yielded (yes - I've since picked up a set of "good" allen sockets). It yielded completly flush with the screw face so there is no way to grasp the nub with anything.
Anyway - I've tried tapping it lightly with a drift (on as much of an angle as I can get) to losen it in hopes that I can get it to drop out - no dice...
Any other suggestions / tips / tricks that I should try before putting it in a padded vice on the drill press and drilling the head off of the screw?
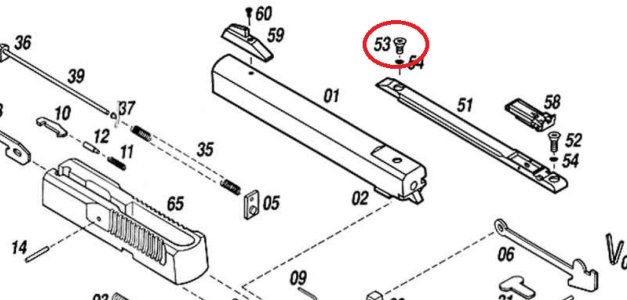
"Someone" snapped the tip of an allen wrench off in the front screw of their Buckmark's site mounting plate (see image below)... Must have been a cheap Chinese tool because there was really very little force applied and it had only deflected a couple of degrees when it yielded (yes - I've since picked up a set of "good" allen sockets). It yielded completly flush with the screw face so there is no way to grasp the nub with anything.
Anyway - I've tried tapping it lightly with a drift (on as much of an angle as I can get) to losen it in hopes that I can get it to drop out - no dice...
Any other suggestions / tips / tricks that I should try before putting it in a padded vice on the drill press and drilling the head off of the screw?
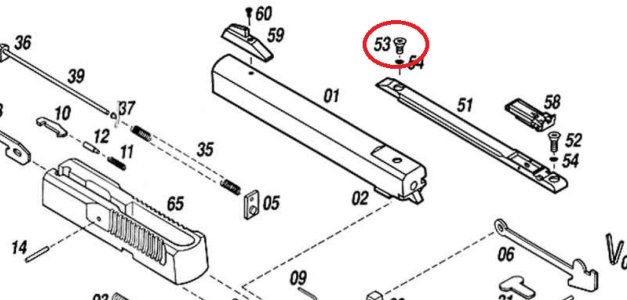